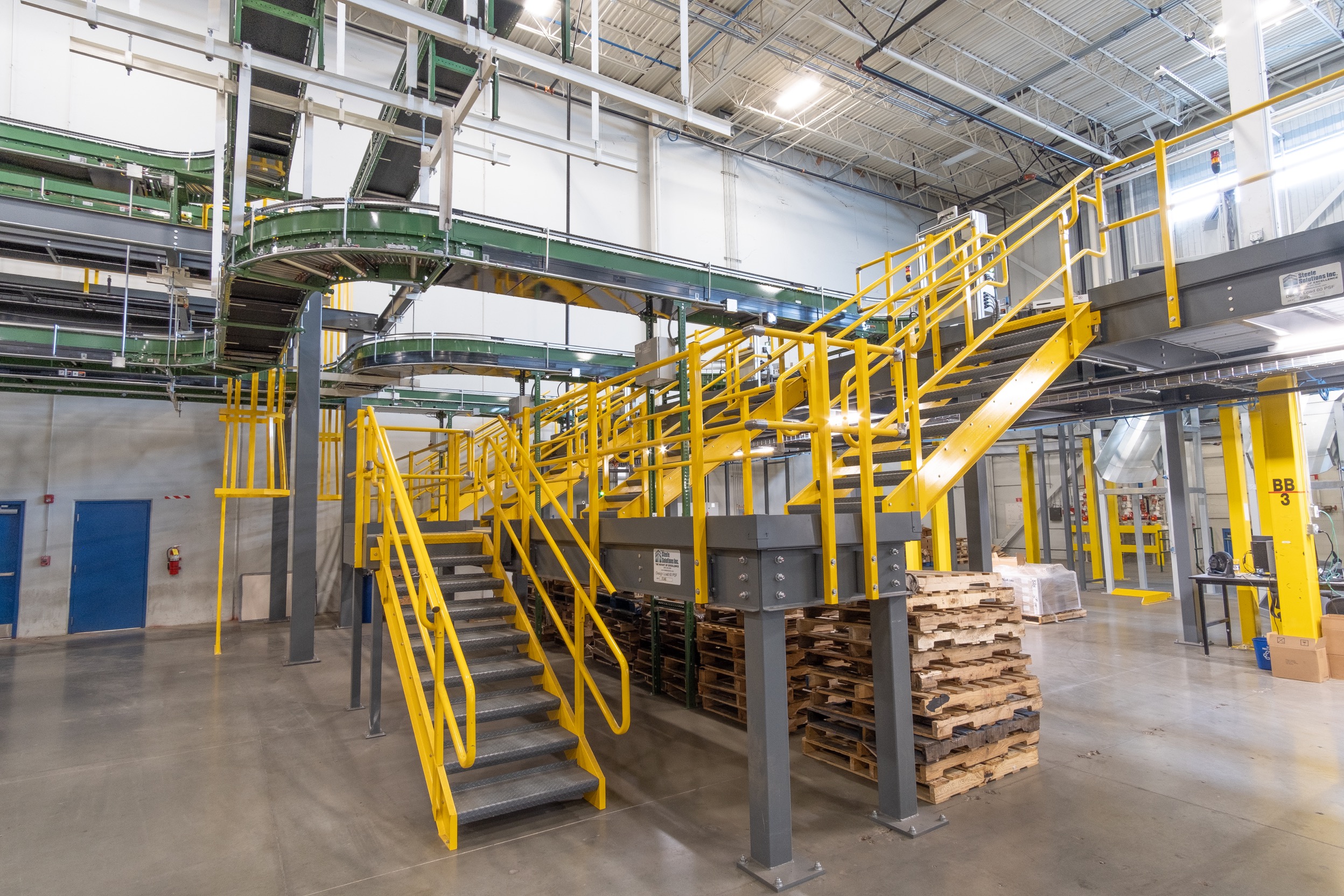
The Cost of a Mezzanine
by Kevin O’Neill
In the material handling business, space is a hot commodity. When an end-user is looking to increase square footage, there are many options that they can consider: buying a new space, expanding/building on to the existing space, or adding an additional structure. Often, new structures are not the first thought, but installing a work platform can double the space in the facility by using the vertical space available. After looking at all the options, if a work platform is the best choice, the question that comes up is, “How much does it cost to build a mezzanine level?” The answer is not as simple as a uniform dollar amount but a combination of many different factors. In this technical tip, we will break down the various features that go into the cost of your new mezzanine level.
Deck Width and Length
The first factor that drives the cost of a mezzanine is the size platform you are adding. The larger the platform, the more materials that will be needed to build the new structure. The larger that platform, the more columns and beams are required to support the new structure. The width and length of the deck will also impact the price for the type of flooring needed to cover the platform. The type of flooring used will also have an impact on the cost. Building a mezzanine and pricing is based on price per square foot can be a much more cost-effective strategy since you will be doubling the space you already have rather than renting or purchasing additional space in another facility.
Height
Along with the deck width and length, the height of the structure will influence the cost of the mezzanine level. The size of the columns will increase the overall material cost. A platform 12 feet off the ground will cost more than a platform 5 feet from the ground due to increased materials needed. Accessing the new level will require the addition of stairs or ladders, another additional cost. Height will also influence the stair system since a taller structure will require more steps and landings for safety.
Overall Design
In a perfect world, all work platforms would be a uniform size and shape. Steele Solutions knows that a standard rectangle shape is not always the solution that is required. At SSI, we work with each customer to design a platform specifically for their space and meet their standards. When designing structures of different shapes, sizes, and floor plans, the cost of materials can increase, impacting the overall cost of the mezzanine floor. Column placement underneath a mezzanine can be affected when creating a specific design of a mezzanine. One plan can require more columns than another. The use of the support structure can also impact the design, impacting the price.
PSF (Pounds per Square Foot)
One of the most significant factors in the design and pricing of a support structure is pounds per square foot. For a typical platform that Steele Solutions designs, the standard load will be 125 PSF. Calculating PSF is directly impacted by the use of the platform – a platform that will be used for storage will require less of a design load than a platform used to hold heavy machinery or equipment. Whenever PSF increases, the platform’s design will need the size of horizontal beams to increase to support the additional load. This will increase the overall cost of the mezzanine.
Custom Features
Every structure is built to serve a specific function, and the function must be met to benefit the end-user. Functions of a platform can include warehouse storage, equipment platform, conveyor, or work platform. Each function will require different features to work correctly, impacting the final cost of a mezzanine. Steele Solutions can include various accessories that can be used for a variety of different outcomes. Most platforms will require handrails and railings around the deck and gates to access the platform. Other features can include stairs (with and without landings), ladders, catwalks, and crossovers. Having these accessories can increase the cost of the mezzanine level but are crucial to the safety and final design of the structure.
Code
The last factor that we will be discussing is the effect building codes will have on the overall design and cost of the mezzanine. Steele Solutions works with IBC and OSHA codes when designing new structures. OSHA focuses on structures accessed by employees and ensuring they have the proper design requirements, such as stairs, ladders, and fall protection. The accessories needed for this will impact the cost. IBC (International Building Code) is the minimum building requirement for all structures and is adopted in all US States. Along with IBC and OSHA, different states, cities, and countries will have their safety and building requirements that may require extra materials and increase the mezzanine floor cost.
Understanding all the factors that can impact the price of a new structure is essential for the decision-making process. Many factors need to be taken into consideration, and it can be an overwhelming and time-consuming process. Steele Solutions is here to help you determine the best design for your space and ensure that it meets all safety and functional requirements while considering project scale and cost.