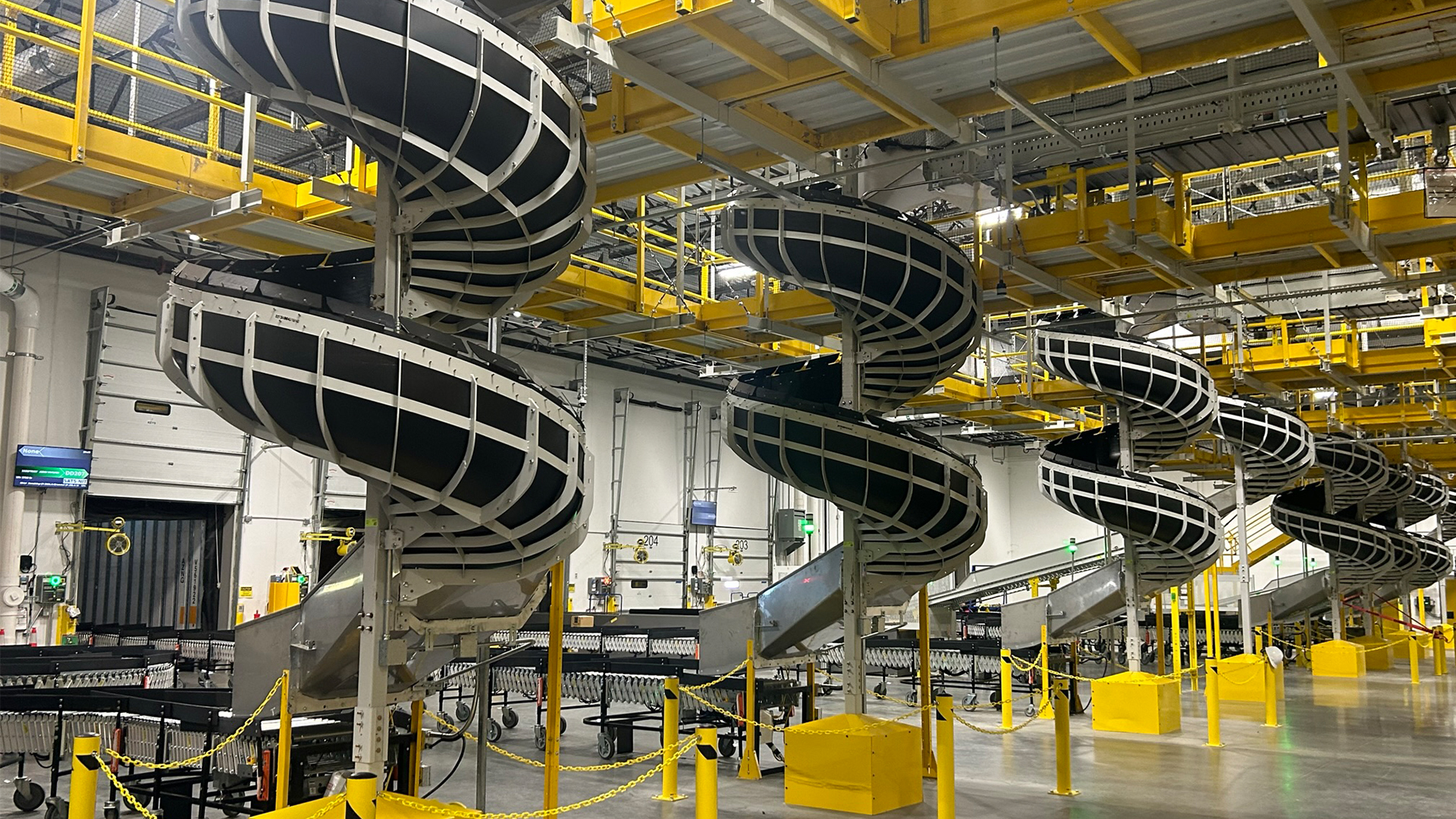
Maximizing Package Flow Efficiency with Custom UHMW and Steel Gravity Chutes
Simple, cost-effective, and versatile, gravity chutes have evolved from basic slides to customized material handling systems that improve efficiency, accuracy, and scalability. In this article, we’ll discuss several advances in gravity chute design.
The Importance of Early Design Collaboration
Many factors can affect gravity chute configuration, placement, and performance: process objectives, process layouts and workflows, structural elements (lighting, fire suppression, pillars, stairs, etc.), and product configuration and packaging. That’s why optimal material handling solutions don’t come from a catalog; they grow out of concepts fueled by collaboration. Working with the right service partner from the very beginning of a project ensures optimal design, seamless integration, and reliable long-term performance.
Steele Solutions combines your ideas and vision with our expert engineering and advanced technologies to create customized solutions that fit your process and facility needs.
“Solutions is in our name. Even if you have a design on a napkin, we can bring it to life.” – Kevin O’Neill, Chief Executive Officer
Steele Solutions utilizes 3D project model simulations to simulate a system’s operation and reveal any modifications needed to improve product flow prior to prototyping. Additionally, we can use our building information modeling (BIM) tools to create 3D models and renderings to illustrate how a system would look, fit into, and improve product flow in your facility.
The Role of Factory Acceptance Testing in Ensuring Performance
Factory Acceptance Testing (FAT) is a critical quality assurance process that tests equipment at a manufacturer’s facility before shipping to a customer’s site. FAT programs explore parameters such as product flow, load tolerance, decline angle, and safety features to ensure adherence to design specifications, functionality under expected operating conditions, and compliance with applicable industry and regulatory standards.
Steele Solutions offers factory acceptance testing to confirm design and performance before installation. Testing is done using actual conveyors and recorded with cameras positioned at every relevant angle. Customers are welcome to observe the FAT at ground level, mid-level, or from above and then review test recordings and results to determine any points for improvement. FAT programs are often powerful risk-mitigation tools suitable for large-scale, high-investment projects.
Adapting Steel Chutes for Emerging Technology
Gravity chutes have been a fundamental material-handling tool for decades. However, chutes are continually being adapted to new technologies intended to enhance performance, efficiency, tracking, maintenance, compliance, and safety.
It is crucial to have an equipment partner who understands the nuances of material handling and continually explores opportunities to adapt traditional gravity chutes with emerging technologies.
Steele Solutions leads the industry in new technology adaptations for gravity chutes. Ultra-high molecular weight polyethylene, UHMW-PE, offers an alternative to steel with high durability and low friction that helps packages move more efficiently. Steele Solutions’ design team excels at integrating robotics and advanced automation systems and modifying chute configurations to adapt to new sorting technologies.
New Sortation Technology
Automated sortation systems redirect packages based on specified parameters such as size, weight, or destination. Integrating advanced sorting technologies allows facilities to enhance throughput and improve accuracy without additional personnel or space.
Here are a few new technologies we often work with:
- Tilt Tray Sorter – a series of trays mounted on a linear or continuous loop conveyor able to tilt and discharge packages in one or both directions into a designated chute. Suitable for various package sizes, weights, and weights, tilt tray sorting provides high-speed sorting and gentle product handling, maximizing efficiency and minimizing product damage (from dropping into the chutes). Integrating tilt tray sortation with gravity chutes also increases space efficiency by utilizing vertical space for sorting rather than expanding the sorting area’s footprint.
- Cross Belt Sorter – a small, independently operated conveyor belt running perpendicular to a main conveyor belt able to divert packages off of the primary conveyor into a chute. These sorters are suitable for a wide range of product sizes and shapes except for items that might roll (e.g., balls, cylinders, etc.), and offer even more gentle handling than the tilt tray sorter. High precision allows cross belt sorters to accurately feed multiple chutes even at high speeds.
- Robot Sorter – mechanical arms or autonomous mobile robots (AMRs) utilizing sensors or vision systems to identify and relocate packages from a conveyor to a chute. Robot sorters are versatile systems that are easily integrated into existing processes and adapted to chute placement, height, and angle.
- Shoe Sorter – a conveyor-based sorting system that uses sliding “shoes” mounted on tracks to push packages gently off the conveyor and into a designated chute or destination. Shoe sorters are ideal for handling items of varying sizes, shapes, and weights and routing packages to multiple destinations, making them highly versatile for distribution centers and warehouses. They are particularly effective for high-speed operations, maintaining accuracy and minimizing product damage during sorting.
Steele Solutions is continually exploring new approaches to integrating sortation technologies with gravity chutes to enhance material handling capabilities and position facilities to meet increasing demands for rapid, accurate order processing.
Automatic Takeaway Technology
Automatic takeaway systems streamline product flow and ensure that discharged packages are quickly routed to their appropriate destination.
Smart conveyor systems at the base of a chute combine sensors, control software, and variable speed and direction to sort and route products based on real-time data. Robotic arms equipped with sensors, vision systems, and specialized grippers can quickly and accurately collect packages as they exit a chute. Mobile robots called Automated Guided Vehicles (AGVs) can be positioned at a chute’s discharge point to collect and transport packages to a designated location.
Steele Solutions’ engineering team works with facilities to ensure seamless integration of automatic takeaway systems to existing chutes and new chute system designs.
How Steele Solutions’ Chutes Solve Key Operational Challenges
We believe that what’s behind our products keeps us at the forefront of the package movement industry. New customers choose us when they need superior design and performance, and existing customers call us for unparalleled service and support. We’re results-driven problem solvers dedicated to understanding our clients’ needs and providing creative solutions to their challenges.
Reducing On-Site Issues with On-Site Field Management Services
Steele Solutions’ on-site field management services focus on mitigating problems associated with receiving, installing, and maintaining new equipment. From assisting with shipping schedules to assessing blueprints and advising on installation sequences, our project managers ensure painless installation, seamless integration, and flawless final inspection.
We can also perform our own installations and manage your project on-site from beginning to end. We foster a strategic partnership fueled by communication and our commitment to providing solutions that fit your needs and improve your facility’s efficiency. Our on-site field management services provide additional support as needed to ensure smooth installation and the mitigation of any issues that might arise.
Offering Assembled Shipments for Installation Efficiency
Unlike competitors’ products that are shipped in pieces and assembled onsite, Steel Solutions can ship gravity chutes fully assembled except for the product entry and exit, which are easily and quickly attached.
In addition to dramatically reducing installation time (over 60% reduction compared to the competitor’s product) and cost, having your chute assembled by our team of experts in our facility reduces on-site labor needs and improves the equipment’s durability and lifespan.
Combining decades of experience and a commitment to understanding customers’ needs, Steele Solutions provides the design, construction, installation, and service guaranteed to meet your performance requirements and exceed your expectations.
To learn more about customized gravity chutes, visit our steel chute product page or contact our team today!