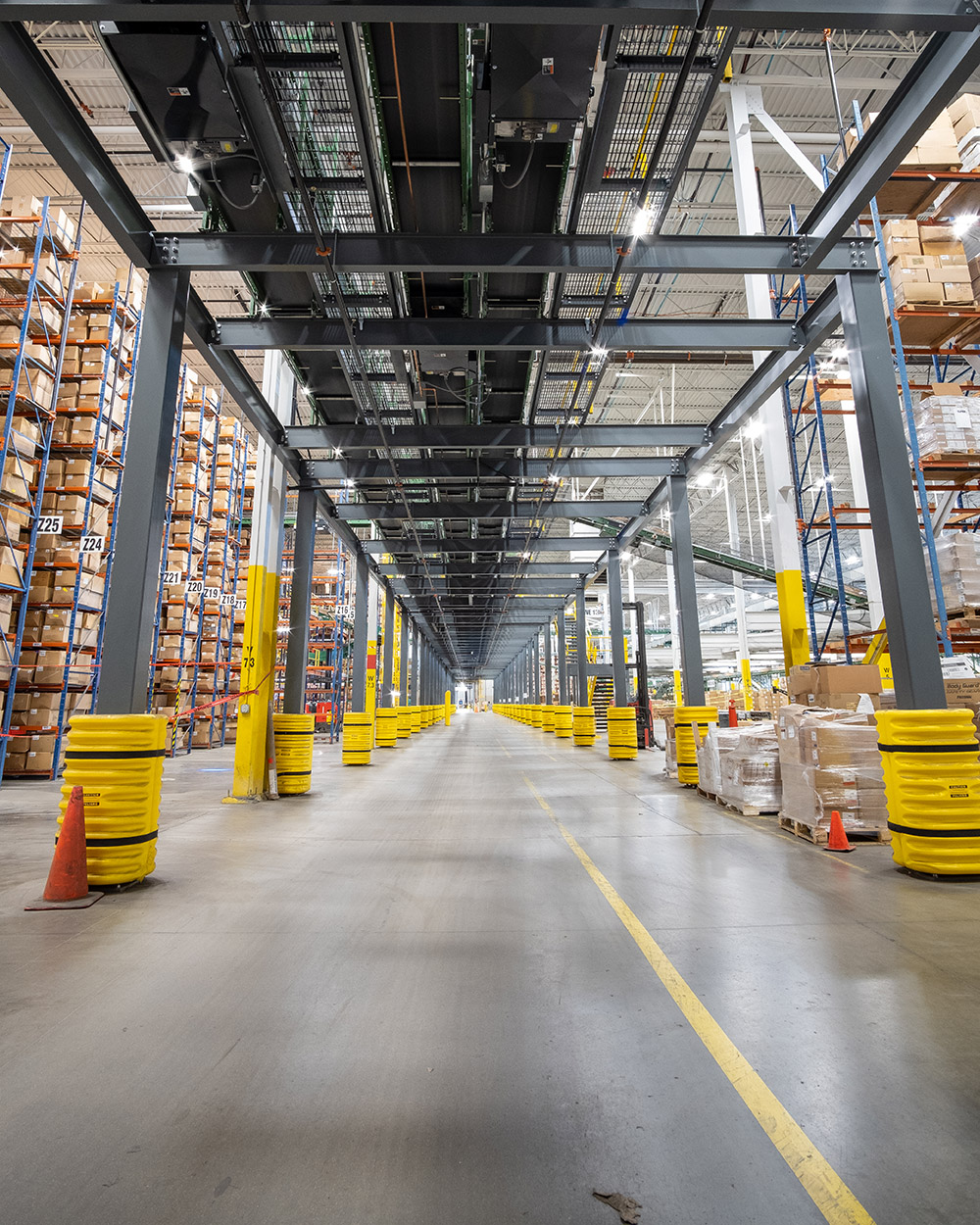
Deflection and Drift
by Kevin O’Neill
An equipment platform’s design needs to satisfy two significant constraints to meet code: Strength and Serviceability. Designing for strength ensures that the platform will resist all the required load combinations for vertical and lateral loads without exhibiting any failure. In addition to meeting the strength requirements, the individual members and structural system must also meet specific serviceability requirements. Serviceability is the acceptable amount of deformation under the daily use of the platform. The equipment platform’s performance is typically examined by the serviceability of the structure and the human comfort associated with it.
Deformation can be expressed in deflection, which is associated with vertical loads, and drift, which is associated with lateral loads. Deflection is the vertical displacement of a beam or floor system. Deflection is a relationship between the amount of gravity load, the span of the structural member, and the moment of inertia of the structural member. The moment of inertia is a shape property of the member that resists bending and reduces the deflection. The higher the moment of inertia, the smaller the deflection. The most efficient manner of providing a higher moment of inertia is with a deeper member.
However, to avoid having oversized framing, an acceptable level of deflection is defined by code. The amount of deflection as a ratio of the span (L) is measured at two different loading levels: total load and live load. The deflection limits by code are L/240 for total load and L/360 for live load for simple span beams. Floor systems (i.e., deck, bar grating, and floor plate) have different deflection requirements based on human comfort. The recommend deflection limit is 1/4″ since the floor system’s deflection would be the most likely deformation that an occupant would experience.
The lateral movement, also known as drift or sway, is a relationship of the amount of lateral load, the height of the structure, and the lateral force-resisting system (LFRS). Braced frames are the most efficient for resisting lateral movement but require the most coordination to avoid bracing members from clashing with equipment. Typically, equipment platforms have moment frames for the LFRS to avoid clashes with equipment and maximize the usable area underneath the platform. The moment of inertia or depth of the columns is the primary factor for resisting the drift motion in a moment frame.
Lateral loads can be generated from human motion, equipment, wind, and/or seismic activity. The acceptable drift limits are associated with the type of lateral loading—the more frequent the lateral load, the smaller the allowable drift. Drift due to seismic loads has the maximum allowable limit since a seismic event’s probability and frequency is the lowest. The strictest drift limits are associated with human motion.
Another concern with lateral movement is the differential drift between adjacent platforms or platforms and the building structure. Gaps between the structures must be provided to avoid potential collisions under extreme events.
Equipment sensitive to deflections and platforms with large amounts of human traffic has different performance requirements than a platform with little human activity or storage platforms supporting mostly static loads. The performance of the structure is the most crucial aspect of the equipment platform over its life cycle. To ensure proper design and the most efficient platform, establish the performance criteria with the design engineer, and define acceptable deflection and drift levels.