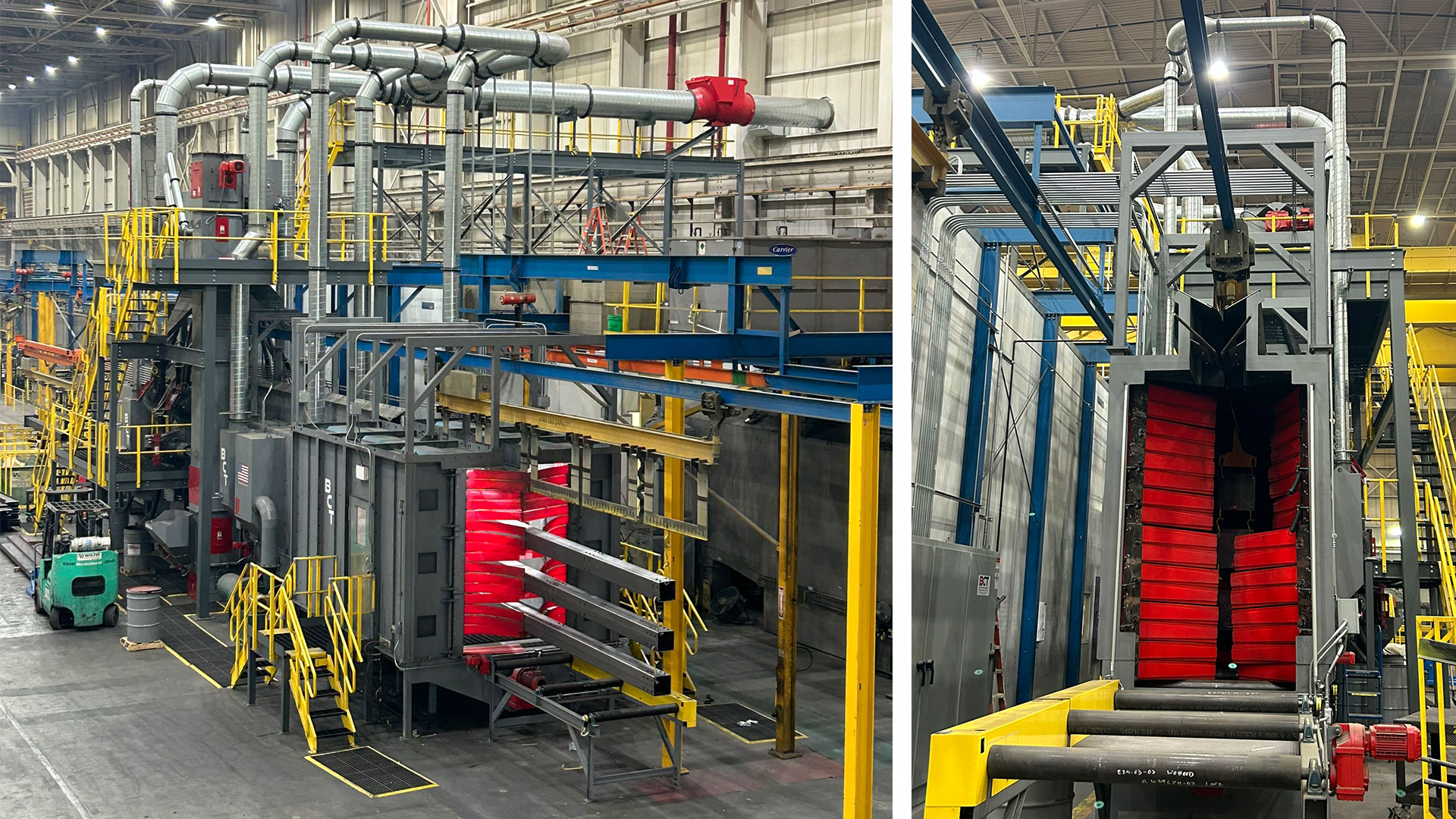
Blast Cleaning: Why Surface Preparation is Critical for Structural Steel Coating Durability
When evaluating structural steel platforms and mezzanines, most facility managers, architects, and project integrators focus on load capacity, design specifications, and installation timelines.
However, there’s a critical factor that often goes overlooked until problems arise: surface preparation prior to coating application.
The integrity of your structural steel installation doesn’t just depend on engineering calculations and fabrication precision—it hinges on invisible factors happening at the microscopic level where paint meets metal.
This article examines why surface preparation matters for teams responsible for specifying, installing, or maintaining structural steel platforms, and how proper surface preparation with blast cleaning translates directly to reduced maintenance costs, extended service life, and enhanced aesthetic durability for your facility investments.
Understanding Surface Preparation in Steel Manufacturing
Steel arrives at manufacturing facilities carrying contaminants from its production journey. Fresh from the mill, structural steel is often coated with mill scale—a bluish-black oxide layer formed during hot rolling. This creates significant adhesion problems for coatings. Rust can also form beneath the scale, depending on the environment.
Most coating failures aren’t due to defective paint or improper application—they’re the direct result of inadequate surface preparation before the first coat of paint was even applied.
Beyond mill scale, steel components face contamination at multiple points:
- Mill oils and lubricants applied during production remain on surfaces
- Environmental exposure leads to oxidation and rust formation, particularly when steel is stored outdoors
Fabrication processes also introduce additional contaminants:
- Welding operations produce slag and residue
- Plasma cutting creates dross (solidified molten metal)
- Machining processes leave behind oils and metal particles
- Handling introduces fingerprints and organic contaminants
These invisible threats create a barrier between the steel substrate and any applied coating. When paint is applied over these contaminants, it adheres to the contamination layer rather than forming a direct bond with the steel itself.
Why Coating Failures Trace Back to Surface Preparation
Sherwin Williams reports that approximately 80% of all coating failures can be directly attributed to inadequate surface preparation.
Common coating failures resulting from poor surface preparation include:
- Delamination: complete separation of the coating from the substrate.
- Blistering: The formation of bubbles as contaminants react beneath the coating.
- Premature rusting: An accelerated corrosion where contaminants create pathways for moisture.
- Flaking and peeling: A progressive coating breakdown starting at contamination points.
These failures typically begin at a microscopic level but quickly expand into visible defects. What makes this particularly problematic for structural platforms is that failures often initiate in hard-to-inspect areas like corners, joints, and underside surfaces.
Proper blast cleaning achieves what no other cleaning method can: complete removal of embedded contaminants while simultaneously creating an optimal surface profile for mechanical adhesion.
What is Blasting?
Blast cleaning, at its core, is a method of propelling abrasive media at high velocity against a surface to remove contaminants and create an optimal profile for coating adhesion.
Unlike chemical treatments that may leave residues or manual cleaning methods that often miss embedded contaminants, blast cleaning physically strips away surface impurities while simultaneously texturing the metal for superior coating adhesion.
At Steele Solutions, we’ve made this critical first step a centerpiece of our quality assurance process because we understand that long-term performance begins with proper preparation.
Steele Solutions’ investment in a state-of-the-art 12-wheel monorail blast system represents our commitment to coating integrity from the foundation up. Let’s examine how this system works and why its implementation matters to your structural platform projects.
How Mechanical Shot Blasting Works: A Three-Step Process
The 12-wheel monorail blast system at Steele Solutions uses shot blasting to transform contaminated steel into an ideal surface for coating.
Here’s how it works:
- Media Delivery System: Steel shot (hardened steel particles) is gravity-fed through steel tubes into high-speed centrifugal wheels.
- Acceleration Mechanism: Twelve strategically positioned wheels spin at high velocity, mechanically propelling the blast media against the steel components passing through the system.
- Impact and Cleaning Action: Upon impact, the steel shot performs two critical functions, it simultaneously removes contaminants like mill scale, rust, oils, and fabrication residues, while also creating a uniform textured surface profile that enhances coating adhesion.
- Continuous Operation: Components move through the system at a controlled rate of 12 feet per minute, ensuring consistent treatment across all surfaces.
- Media Recycling: The system continuously collects, filters, and recirculates the blast media, separating contaminants and ensuring consistent blasting performance.
Unlike manual blasting or outsourced pre-blasting, this automated system ensures complete consistency from component to component, eliminating human variability and ensuring that every square inch of steel receives identical surface preparation.
Substrate Quality Immediately Before Painting Affects Paint Performance
Think of substrate preparation as the foundation of a building; no matter how premium the materials used above, a compromised foundation results in undesired results.
The quality difference becomes evident over time: structures with proper surface preparation maintain their appearance, while improperly prepared surfaces show premature coating breakdown, requiring costly maintenance and potentially compromising structural integrity.
For facility managers and project stakeholders, understanding this relationship translates directly to long-term cost implications. Surface preparation dramatically influences lifetime maintenance expenses and facility appearance.
Achieving SP10 Near-White Surface Finish
Surface preparation standards provide a common language for specifying and verifying cleanliness levels. Steele Solutions’ blast system is capable of achieving an SP10 near-white metal finish—one of the highest cleanliness standards in the industry and the optimal preparation for structural components.
An SP10 finish means:
- At least 95% of each square inch is free of all visible residues
- Only slight staining or slight discoloration is permitted
- No visible oil, grease, dirt, mill scale, rust, or coating remains on the surface
This level of cleanliness significantly exceeds typical industry standards for structural steel components. While many manufacturers settle for SP6 commercial blast (which permits some staining and shadows), our SP10 capability substantially improves coating adhesion and longevity.
The difference becomes particularly important in:
- Environments that experience frequent temperature or humidity changes
- Facilities with exposure to chemicals or corrosive elements
- Applications where aesthetic appearance must be maintained long-term
- Structures where access for maintenance is limited or costly
For architects and facility planners, this translates to specifying components with significantly extended coating life and reduced maintenance requirements.
How Does Blasting Integrate with the Painting Process?
What truly sets Steele Solutions’ approach apart is the strategic integration of blast cleaning within the overall painting process. Unlike other manufacturers who may purchase pre-blasted steel or send components out for blasting, our monorail system is incorporated directly into our paint line as the first operation.
The complete integrated process follows this sequence:
- Component Loading: Fabricated steel components are mounted on the monorail system.
- Blast Cleaning: Components pass through the 12-wheel blast system at 12 feet per minute, achieving an SP10 near-white finish.
- Multi-Stage Wash System: An initial wash removes any remaining particulates. Multiple rinse stages are completed to ensure complete surface preparation.
- Drying: Components pass through a forced-air dry-off tunnel, ensuring complete moisture removal before coating application.
- Powder Coating Application: Electrostatically charged powder is applied in a controlled environment.
- Curing: The coated components pass through a curing oven, creating the final hardened finish.
By managing the entire surface preparation and coating process in-house, we maintain quality control from raw material to finished product.
This integrated approach translates to predictable quality and consistent performance across all components, eliminating the variation that often occurs with outsourced processes or partial surface preparation.
Blasting Benefits for Facility Owners and Project Stakeholders
Extended Paint Lifecycle and Reduced Maintenance Costs
Proper surface preparation through blasting significantly extends coating lifespans, delivering exceptional return on investment. By removing all contaminants and creating an optimal surface profile, customers can expect fewer repainting cycles, reduced downtime, and substantial cost savings over the structure’s lifetime.
Enhanced Aesthetic Quality and Professional Appearance
Beyond durability, blasting delivers superior aesthetic results. The uniform surface profile creates the foundation for flawless paint application with consistent texture and appearance. This professional finish not only improves facility appearance but also reinforces brand image and quality perception.
Preventing Common Paint Failure Modes
Blasting systematically eliminates the primary causes of coating failures. By removing all traces of previous coatings, corrosion, mill scale, and contaminants, it addresses the root causes of adhesion problems. This proactive approach prevents the cascading failures that can quickly compromise structural integrity and appearance.
Surface preparation quality serves as a visible indicator of a manufacturer’s commitment to excellence throughout their operations.
When a company invests in proper blasting and surface preparation, it demonstrates attention to detail and quality standards that typically extend to all aspects of their business. This commitment isn’t merely cosmetic—it reflects a fundamental understanding that lasting quality begins at the foundation.
Get to Know Steele Solutions
Since 1996, Steele Solutions has been an industry leader in the design and fabrication of steel work platform solutions for distribution facilities. At Steele Solutions, we’ve made blast cleaning a cornerstone of our quality commitment because we understand that superior surface preparation directly translates to extended service life, reduced maintenance costs, and sustained aesthetic appeal for your facility investments.
To learn more or ask a question about your next project, contact Steele Solutions today.